Hyundai Elantra: Air Conditioning System / Compressor
Description and operation
The compressor is the power unit of the A/C system.
It is located on the side of engine block and driven by a V-belt of the engine.
The compressor changes low pressure and low temperature refrigerant gas into high pressure and high temperature refrigerant gas.
Variable Swash Plate Compressor
The compressor has a swash plate that rotates to reciprocate pistons, which compress refrigerant.
The variable swash plate compressor controls the swash plate angle to change the refrigerant displacement. It achieves precise cooling capability control in accordance with vehicle interior and driving conditions.
The externally controlled variable swash plate compressor changes the swash plate angle by an ECV (Electric Control Valve) in accordance with an electrical signal from the heater & A/C control unit.
This enables stable temperature control and improved driving sensation.
ECV Control Diagram
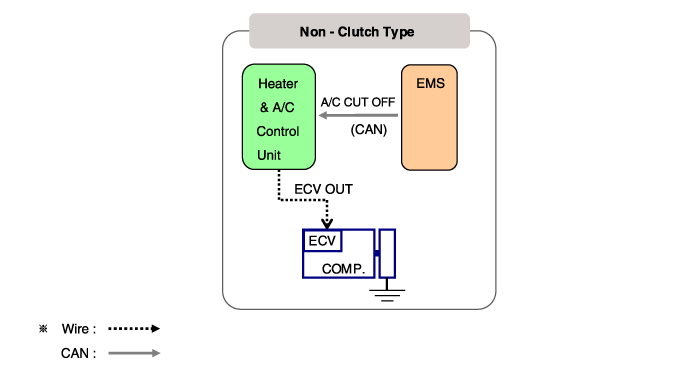
Components and components location
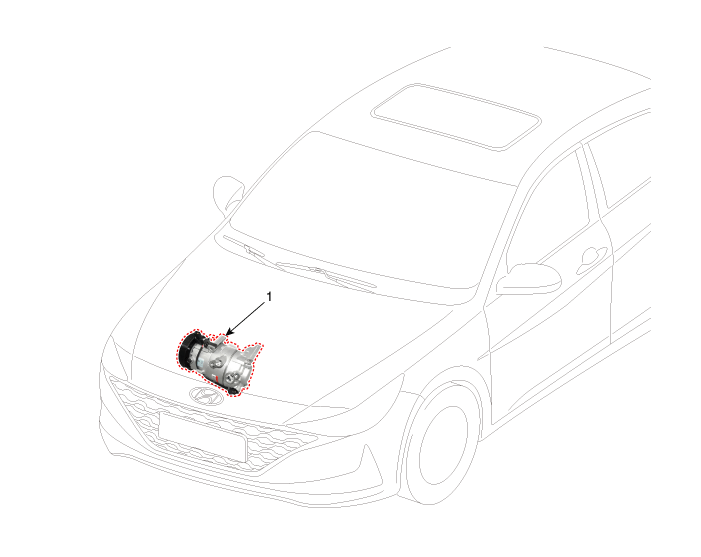
[Gasoline 1.6 MPI]

1. Clutch bolt 2. Disc & Hub assembly 3. Air gap spacer 4. Retainer (A) 5. Pulley 6. Retainer (B)
| 7. Clutch magnetic coil 8. Compressor 9. Electric Control Valve(ECV) Snap ring 10. Electric Control Valve (ECV)
|
[Gasoline 1.6 T-GDI, Gasoline 2.0 MPI NU]
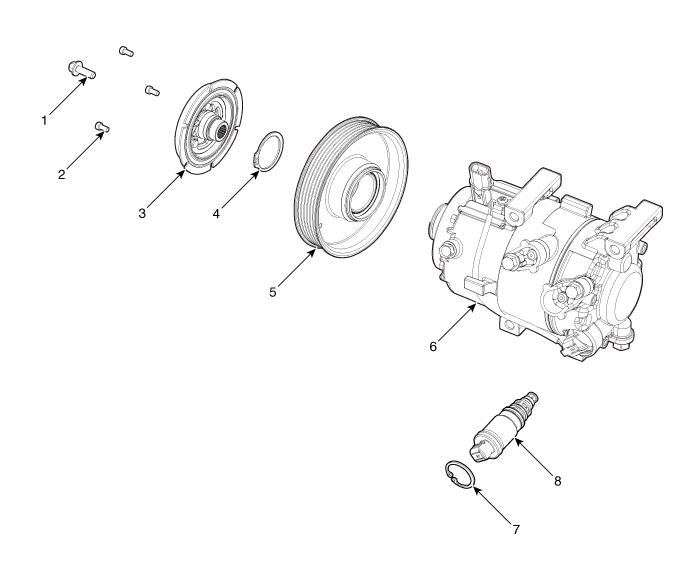
1. Clutch bolt 2. Limiter bolt 3. Disc & Hub assembly 4. Snap ring
| 5. Pulley 6. Compressor 7. Electric Control Valve(ECV) Snap ring 8. Electric Control Valve (ECV)
|
[Gamma 1.6 MPI]
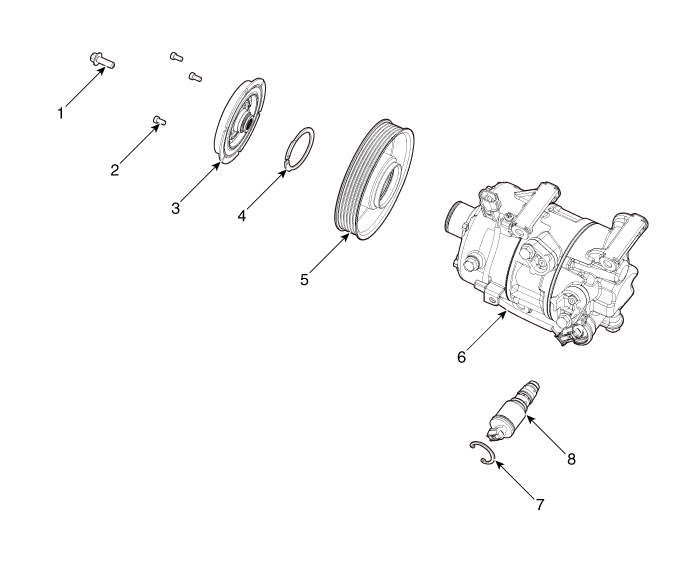
1. Clutch bolt 2. Limiter bolt 3. Disc & Hub assembly 4. Snap ring
| 5. Pulley 6. Compressor 7. Electric Control Valve(ECV) Snap ring 8. Electric Control Valve (ECV)
|
Repair procedures
Precautions for using the plastic pulley •
| Take care not to give physical impact to the plastic pulley. If exposed to the impact of dropping and collision, the pulley should not be used although not damaged. |
•
| Be careful not to place the pulley to downwards of the floor or table. 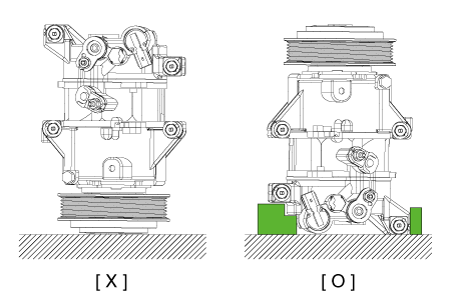
|
•
| Be careful not to apply the external force and impact on pulley while moving or using. 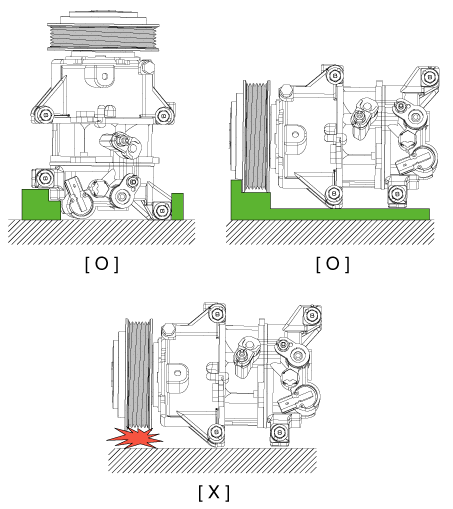
|
•
| Be careful not to apply force to the pulley. 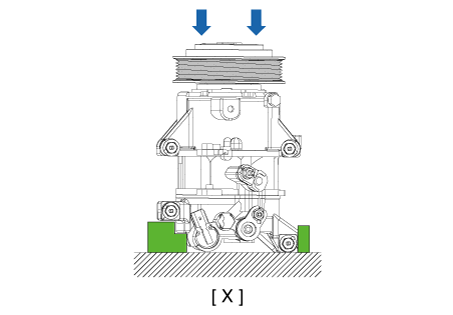
|
|
1. | If the compressor is marginally operable, run the engine at idle speed, and let the air conditioning work for a few minutes, then shut the engine off. |
2. | Disconnect the negative (-) battery terminal. |
3. | Recover the refrigerant with a recovery / charging station. |
4. | Remove the engine room under cover. (Refer to Engine Mechanical System - "Engine Room Cover") |
5. | Remove the front wheel guard. (Refer to Body - "Front Wheel Guard") |
6. | Loosen the drive belt. (Refer to Engine Mechanical System - "Drive Belt") |
7. | Remove the bolts, then disconnect the suction line (A) and discharge line (B) from the compressor. Tightening torque : 8.8 - 13.7 N.m ( 0.9 - 1.4 kgf.m, 6.5 - 10.1 Ib-ft) |
•
| Plug or cap the lines immediately after disconnecting them to avoid moisture and dust contamination. |
|
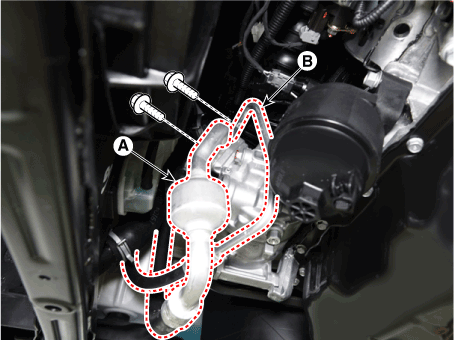
|
8. | Disconnect the compressor switch connector (A). 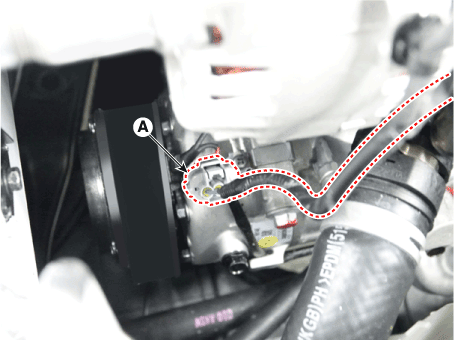
|
9. | Remove the compressor (A) by loosening the mounting bolts. Tightening torque : 20.0 - 32.95 N.m (2.04 - 3.36 kgf.m, 14.75 - 24.30 Ib-ft) |
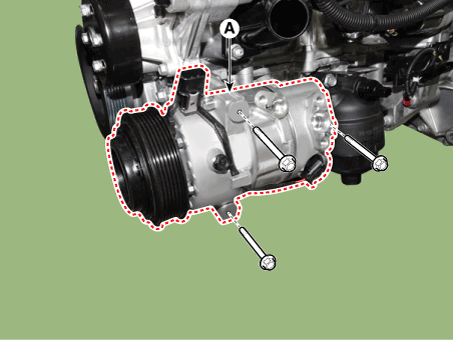
|
1. | Make sure the compressor mounting bolt with the correct length is screwed in. Tighten the mounting bolts with the specified tightening order. Tightening torque : 20.0 - 32.95 N.m (2.04 - 3.36 kgf.m, 14.75 - 24.30 Ib-ft) |
[Gasoline 1.6 MPI] 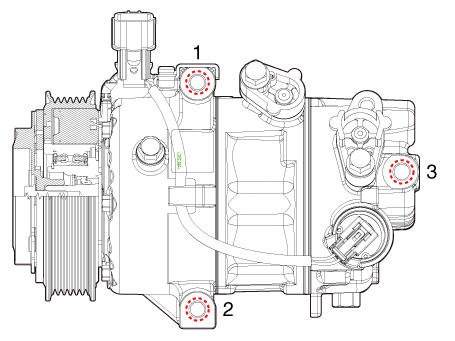
[Gasoline 1.6 T-GDI, Gasoline 2.0 MPI NU] 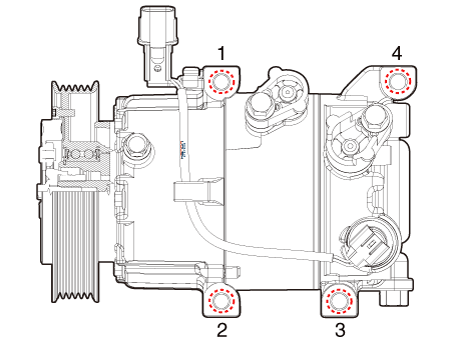
[Gamma 1.6 MPI] 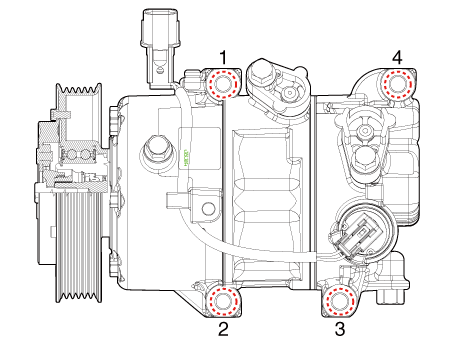
|
2. | To install, reverse the removal procedure. –
| If you install a new compressor, drain all the refrigerant oil from the removed compressor and measure its volume. Subtract the volume of drained oil from the original capacity. The result is the amount of oilcompressor oil you should drain from the new compressor (through the suction fitting). |
–
| Replace the O-rings with new ones at each fitting, and apply a thin coat of refrigerant oil before installing them. Be sure to use the right O-rings for R-134a or R-1234yf to avoid leakage. |
–
| To avoid contamination, do not return the oil to the container once dispensed, and never mix it with other refrigerant oils. |
–
| Immediately after using the oil, replace the cap on the container and seal it to avoid moisture absorption. |
|
1. | Check the plated parts of the limiter & hub assembly for color changes, peeling or other damage. If there is damage, replace the assembly. |
2. | Check the pulley (A) bearing play and drag by rotating the pulley by hand. Replace the pulley with a new one if it is noisy or has excessive play / drag. 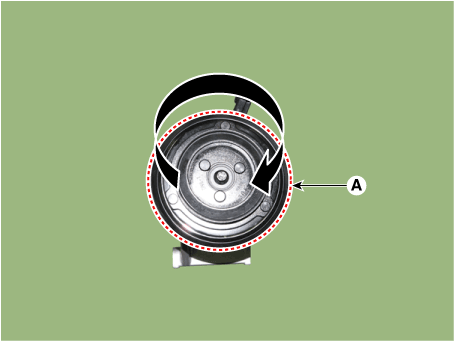
|
External Control Valve Compressor Inspection (Diagnostic tool) |
Compressor type: Fixed type compressor, External control valve, Internal control valve.
In cases of fixed type and internal control valve, it is possible to inspect compressor's operation with clutch noise.
When it comes to External control valve, however, it cannot be checked in this way bacause it doesn't have a clutch.
So, ECV should be inspected with diagnostic tool as below.
1. | Connect diagnostic tool to the vehicle and select 'Aircon Compressor Test(ECV type)' [ECV1] 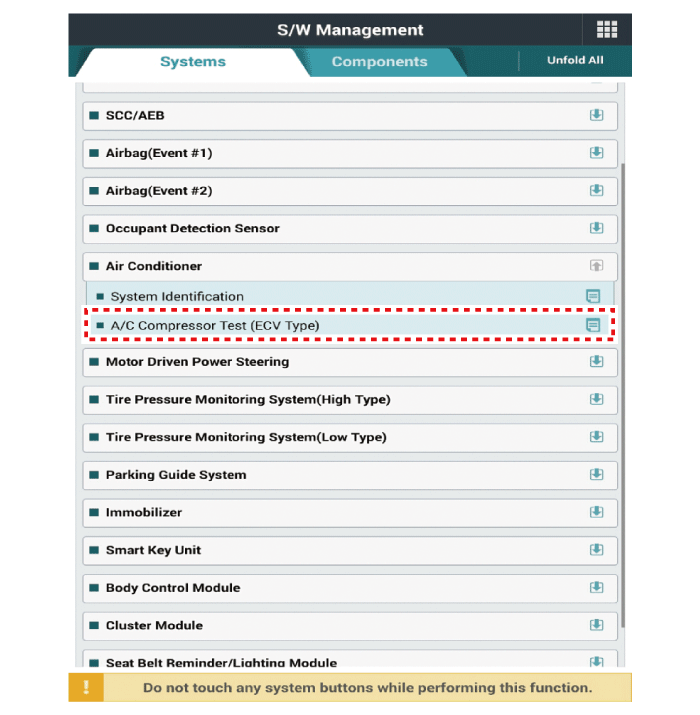
|
2. | Make the vehicle ready as the diagnostic tool instruction on the monitor. (Turn off A/C 'switch' only) 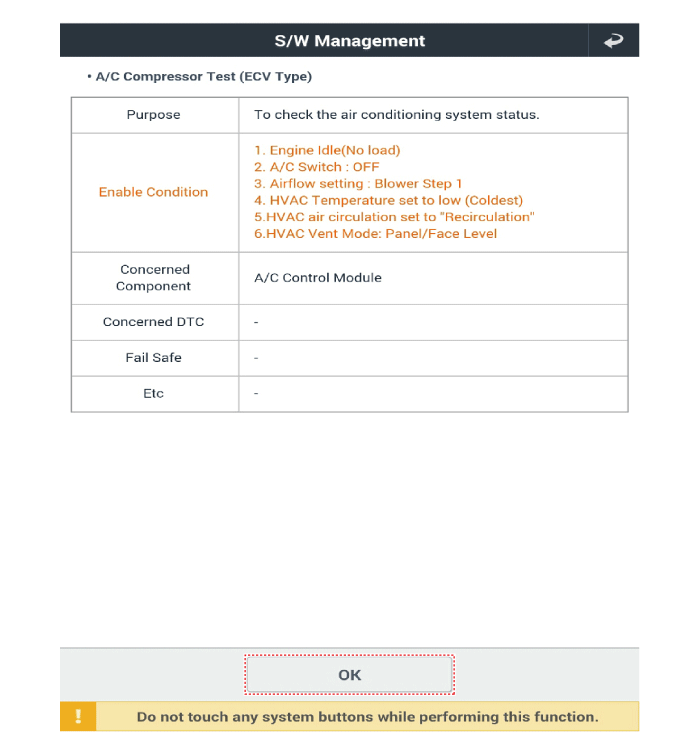
|
3. | Check if other DTC codes are found before inspect ECV compressor. If so, solve that problems first. If not, press 'OK' button to continue. Do not continue inspection if these DTC codes are found: B1241, B1242, B1672, B1685, B1686, B1687 |
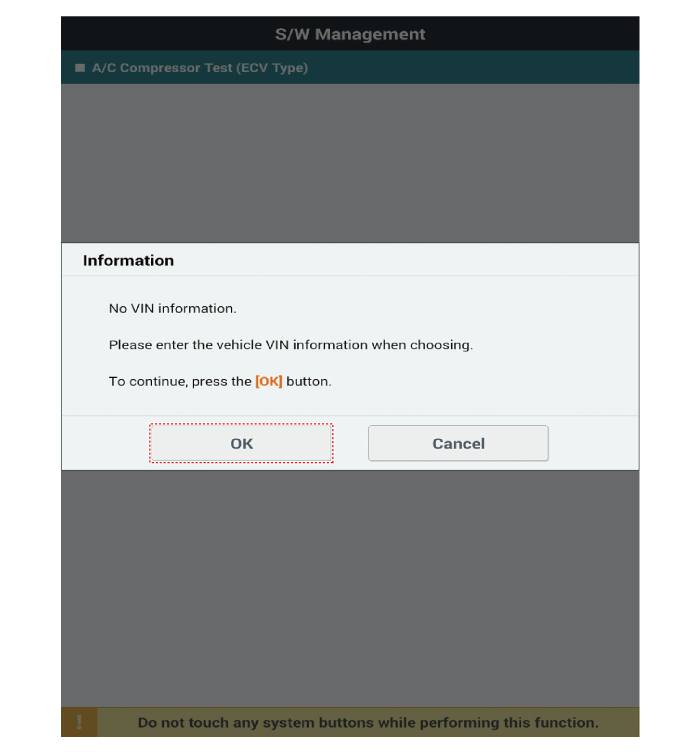
|
4. | Start inspection 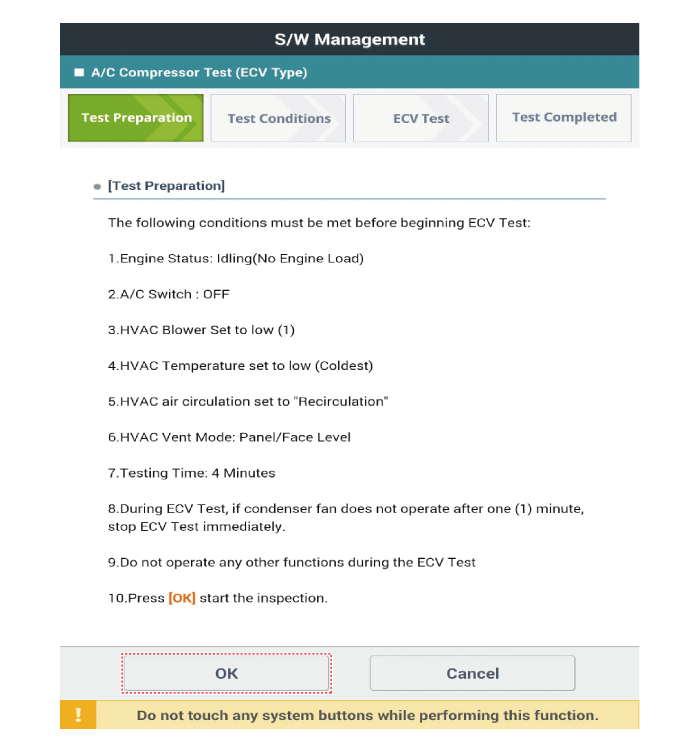
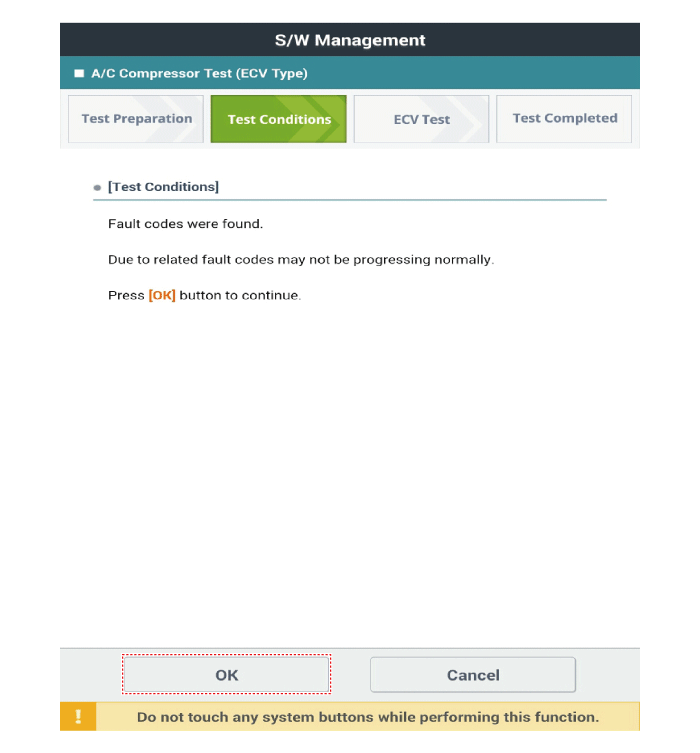
Check if condenser fan is operating when condition is changed to 'ECV running' |
Relief valve will operate if condenser fandoesn't work due to overpressure in thecompressor. It helps the airconditiong system torelieve by releasing refrigerant and oil (losed ifrelieved). ※ Refill refrigerant and oil after operation of relief valve ※ Noise occurred when relief valve is in operation |
|
5. | Check the result of inspection. [ECV7] 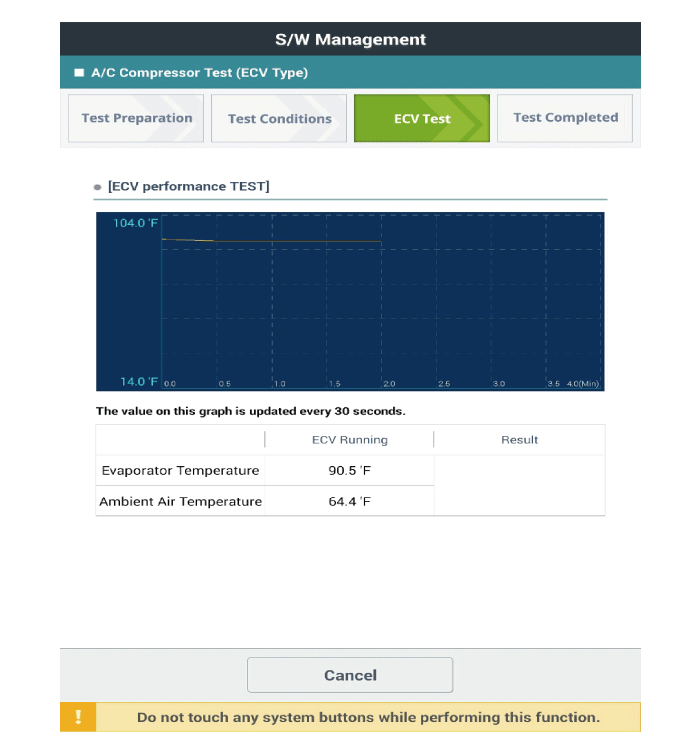
[ECV8] 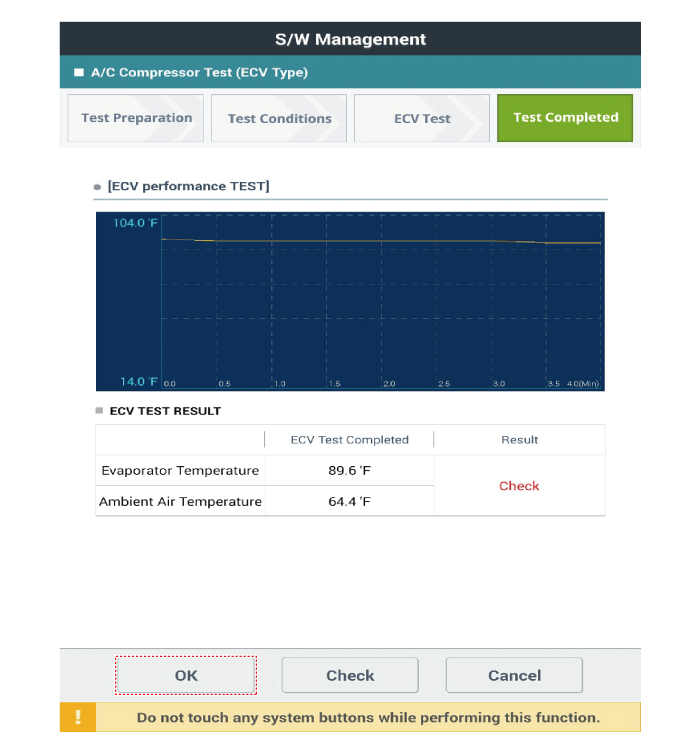
|
6. | If the result shows "Check" , click "Check" and follow the instruction. 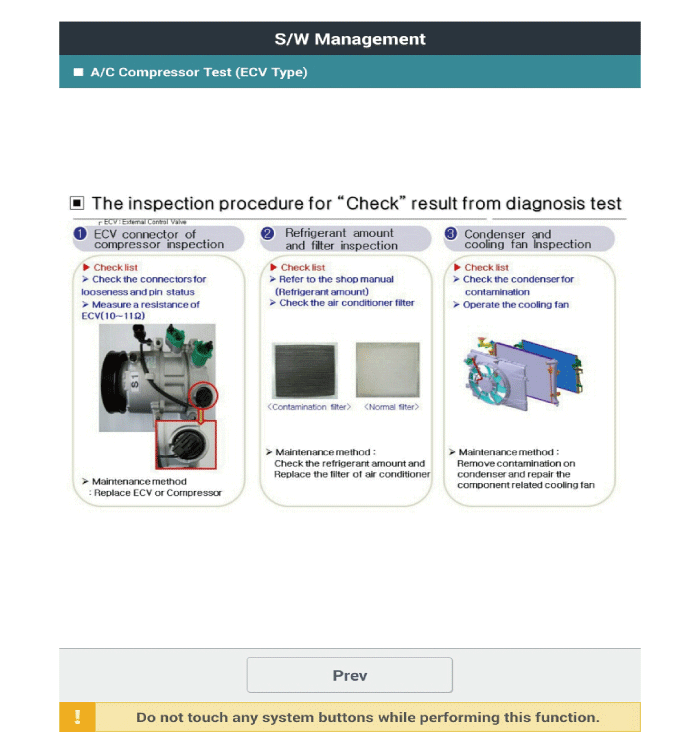
|
7. | Inspect ECV again from the first step. |
1. | Remove the engine room under cover. (Refer to Engine Mechanical System - "Engine Room Cover") |
2. | Remove the front wheel guard. (Refer to Body - "Front Wheel Guard") |
3. | Loosen the drive belt. (Refer to Engine Mechanical System - "Drive Belt") |
4. | Remove the clutch bolt (A) while holding the pulley with a clutch bolt remover (09977-3R000). 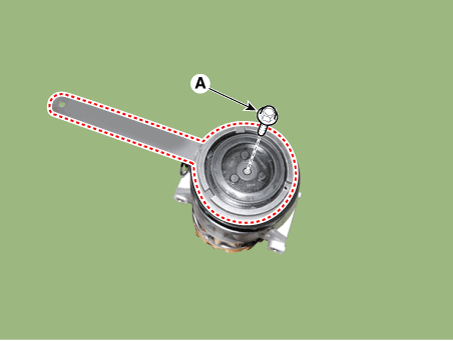
|
5. | Remove the disc & hub assembly (A). 
|
6. | Remove the snap ring (A) with a snap ring plier. 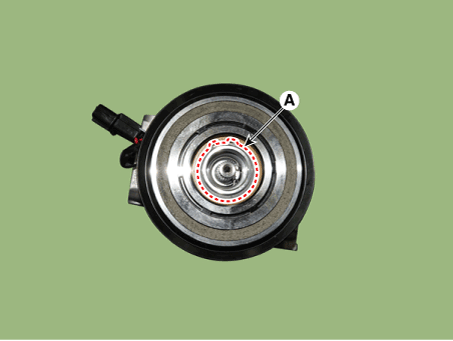
|
7. | Remove the pulley (A). 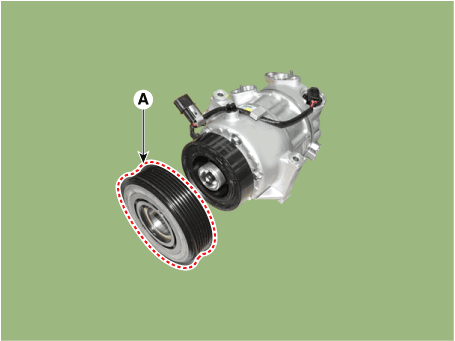
–
| Be careful not to damage the pulley and compressor during disassembly / reassembly. |
–
| Once the snap ring is removed, replace it with a new one. |
|
|
8. | Reassemble in the reverse order of disassembly. –
| Clean the pulley and compressor sliding surfaces with non-petroleum solvent. |
–
| Install a new snap ring, and make sure they are fully seated in the groove. |
–
| Make sure that the pulley turns smoothly after reassembly. |
|
Components and components location
Components Location1. Refrigerant Pipe Assembly
Repair procedures
Replacement1.If the compressor is marginally operable, run the engine at idle speed, and let the air conditioning work for a few minutes, then shut the engine off...
Components and components location
Components Location[General type]1. Condenser[N Line]1. Condenser
Repair procedures
Inspection1.Check the condenser fins for clogging and damage...
Other information:
You should exercise the utmost care
to prevent damage to your vehicle and
injury to yourself whenever performing
any maintenance or inspection
procedures.
We recommend you have your
vehicle maintained and repaired by
an authorized HYUNDAI dealer...
Blind-Spot Safety system may not
operate normally, or the system may
operate unexpectedly under the
following circumstances:
There is inclement weather, such as
heavy snow, heavy rain, etc.
The rear corner radar is covered with
snow, rain, dirt, etc...